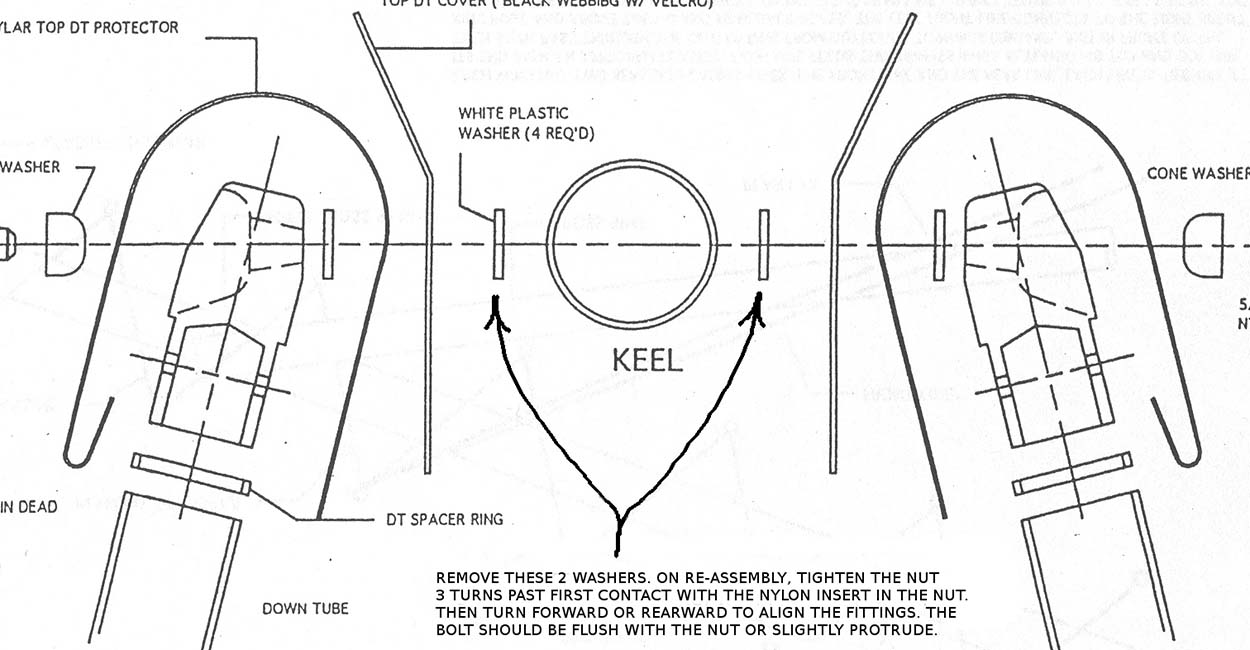
The legendary hang glider acro pilot John Heiney has been flying – and looping – his UP International Predator for 21 years. The official Guinness world record holder for consecutive loops (52) from 1988 to 1998 and four-time world aerobatic hang gliding champion, last week he issued this safety note for his favourite wing. John thinks in 2020 there are “less than 100” UP Predators still flying
On Thursday my student Shawn and I set up at the E. We were the only pilots flying that day. After Shawn launched and got up 1000 over, I was alone at launch. I was hooked into the “Trapezoid Predator” and standing at launch when I remembered that I had intended to put my pocket camera in the holster on my harness. I hesitated at launch because I was ready to go and if I delayed, it might blow down (a not-uncommon occurrence at this launch site).
I decided I wanted the camera. I backed off launch and started rotating the glider left so it wouldn’t blow over while I got the camera out of my car. When it was about 45 degrees to the wind, I felt a pop and set the glider down. It felt as though the left downtube had popped off the keel. How could this be? I looked and confirmed visually that indeed the top DT fitting had come off the control bar apex bolt and was pushing up against the sail!
I had believed since the TRX days that the control bar apex bolt was secure (once installed properly), since the top DT fittings were designed to “cage” the head of the bolt and the nut. There was no conceivable way that the nut could unscrew without rotating one of the fittings. It had just been demonstrated to me that I was wrong about this. I had been(just seconds before) standing at launch, ready to fly a glider that was about to fall apart. My desire to have the camera with me had delayed my flight just long enough to save me from a significant in-flight failure. It’s good to be lucky.
I opened my car, got out some tools and replaced the DT fitting and nut. As I tried to tighten the nut an extra turn, I found that the bolt was indeed rotating in the other DT fitting. As it turns out, during the 21 years I’ve flown this glider, the steel bolt head had worn the aluminum fitting enough to allow rotation. I put the downtube back on, put the camera in the holster(which incidentally, I did not use on this flight) and went flying.
I got up about 1500 over in the recalcitrant thermals of the day, flew about 50 minutes, visited Bedrock and headed out to find Shawn in the LZ, who had soared an hour while I was repairing my glider and struggling to climb-out. I had decided to play it conservative on this flight, so I did only one loop near the edge of the lake as I descended into the LZ. Shawn wondered why it had taken me a half hour to launch after he had departed the mountain. I told him my story as we folded our wings.
Hence forth, I shall check the control-bar apex nut during my pre-flight walk-around. One person foretold this issue. When Joe Greblo started selling Predators and Saturns some 20 years ago, one thing offended his sense of safety on our gliders. It was the fact that the control-bar apex bolt did not extend through the nylock insert in the nut. Joe was right. I was wrong.
Those of you who are still flying a TRX, XTR, XTC, Predator or Saturn, should check the apex nut in the left top downtube fitting during your pre-flight inspection to verify that the end of the bolt is in contact with the nylon insert in the nut. It need not be extending through the nut, just touching the nylon insert. No replacement of the fittings is necessary.
There is a simple fix that you can do to improve the security of your UP/Altair glider’s control bar apex bolt assembly. It is most easily done with the glider on the control bar, the wings spread and the nose lifted by a rope from above.
Procedure: Remove the left downtube from the top downtube fitting. Un-screw the nut by rotating the fitting. Remove the bolt from the keel while leaving it assembled in the right fitting. No need to disassemble the downtube, apex bolt or fitting on the right side. Reassemble without 2 of the 4 plastic washers(as shown in the diagram). This will allow enough space to tighten the nut 3 extra turns after the bolt end contacts the nylon insert in the lock-nut. Then, rotate the fitting (in either direction, whichever is shorter) until the fittings are aligned with each other and re-attach the down tube.
Even with this fix, I advise that we always check this nut in our pre-flight inspection.
I have always felt an obligation to continue to fly this glider regularly (in original configuration) so that if any problems with the design arise, they are likely to happen to me first. I am happy to report that I survived this issue. I have never replaced the bottom side wires on this glider; because, I believe that the exceptional design of the corner fittings will allow no bending stress on the BS cables during set-up and fold-down. I have tested BS cables removed from our gliders after years of service. They all failed at higher than rated breaking strength.
If you have questions, email me at hangglidingphotos@hotmail.com.